While 3D metal printing improves manufacturing efficiency, it also brings challenges to metal powder management. Traditional manual operations are inefficient, difficult to ensure quality, and pose safety risks. Traditional processing methods often rely on manual operations, which are not only inefficient, but also difficult to ensure the quality and consistency of powder, and even hide safety risks.
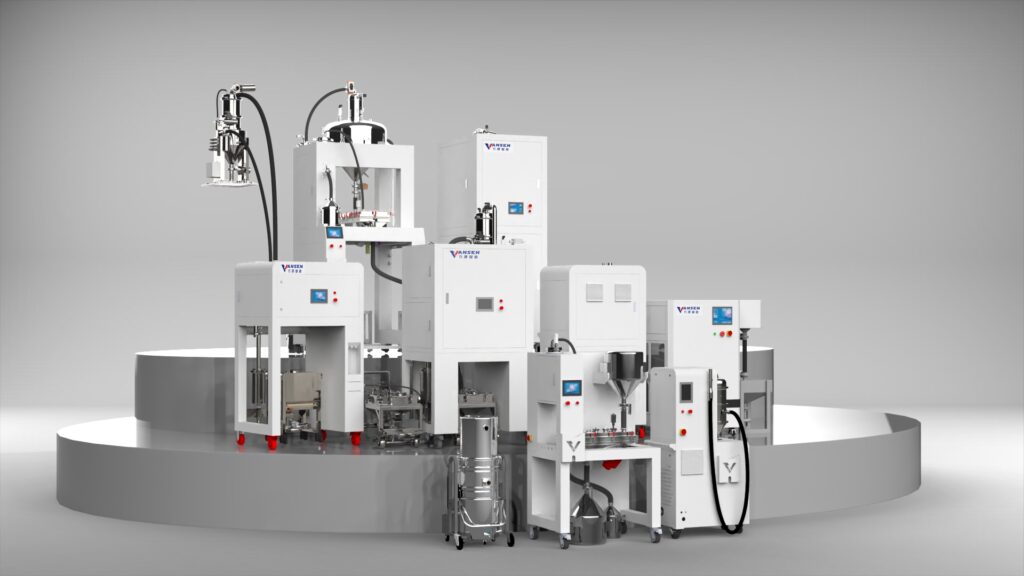
Wansheng has launched a complete set of 3D printing metal powder recycling processing equipment solutions, including suction machines, powder feeders, screening machines, dryers, feeders, suction and screening all-in-one machines and other additive post-processing equipment, which can form a highly targeted, efficient and automated powder circulation management solution based on the actual needs of customers.
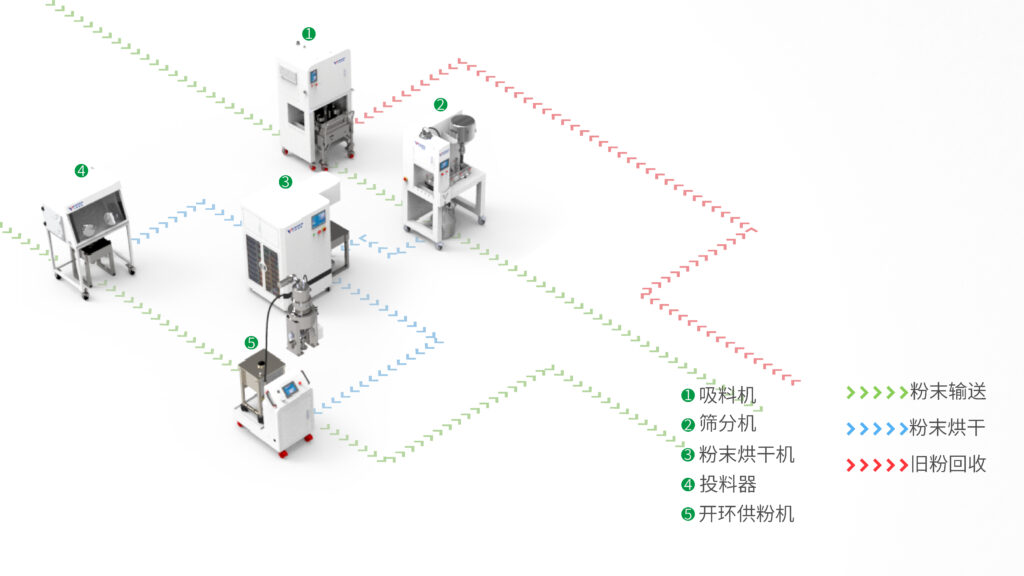
1. Suction machine
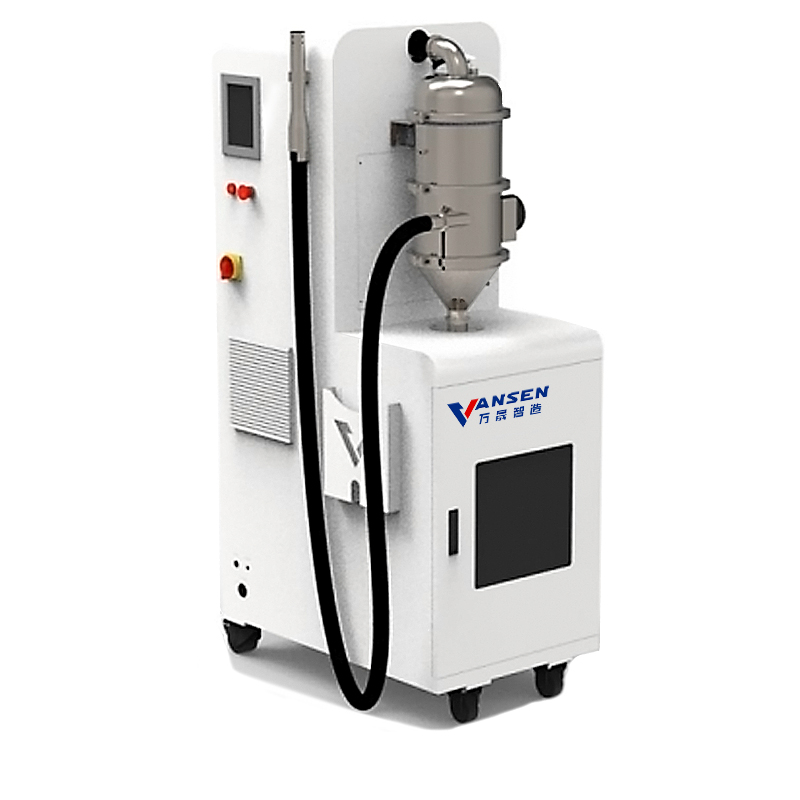
The VAC-220 series material suction machine adopts a structural design that combines cyclone centrifugal separation and high-efficiency filter elements, which allows the powder to be separated into the storage bin under the action of centrifugal force, significantly reducing the workload of the filter element, effectively extending the life of the filter element, and improving the efficiency of the filter element. material efficiency.
2. Screening machine
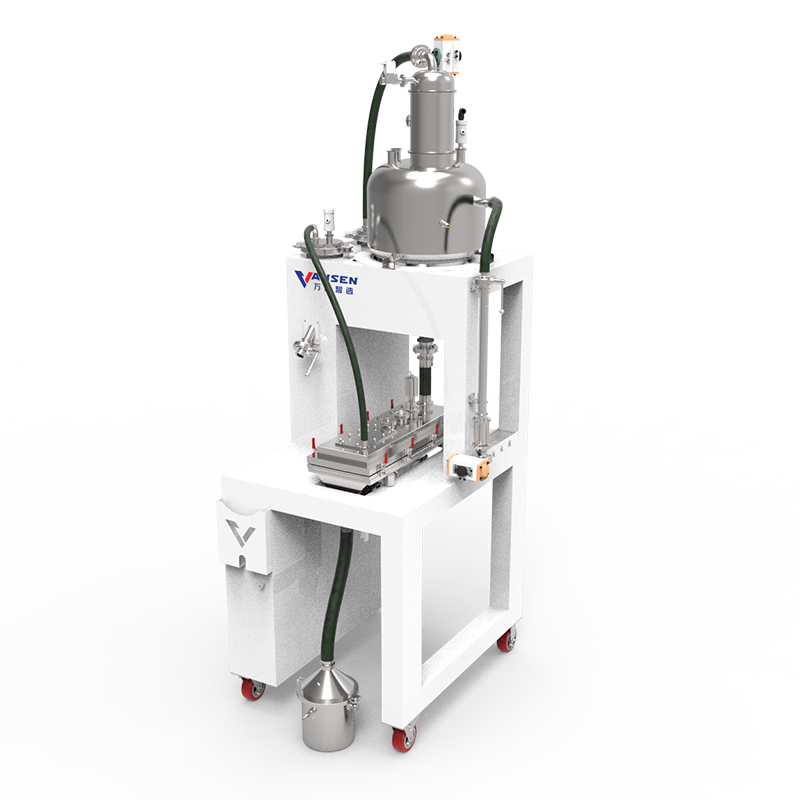
Wansheng launched the APM-S 3D ultrasonic metal screening machine, which is specially developed for large-volume screening. Through the working mode combining the vibration motor with the high-frequency ultrasonic mechanical vibration wave, it can effectively remove impurities and large particles in the powder and ensure the uniform particle size of the powder. It is a new explosion-proof linear screening machine widely used in the 3D printing industry.
3. Suction and screening machine
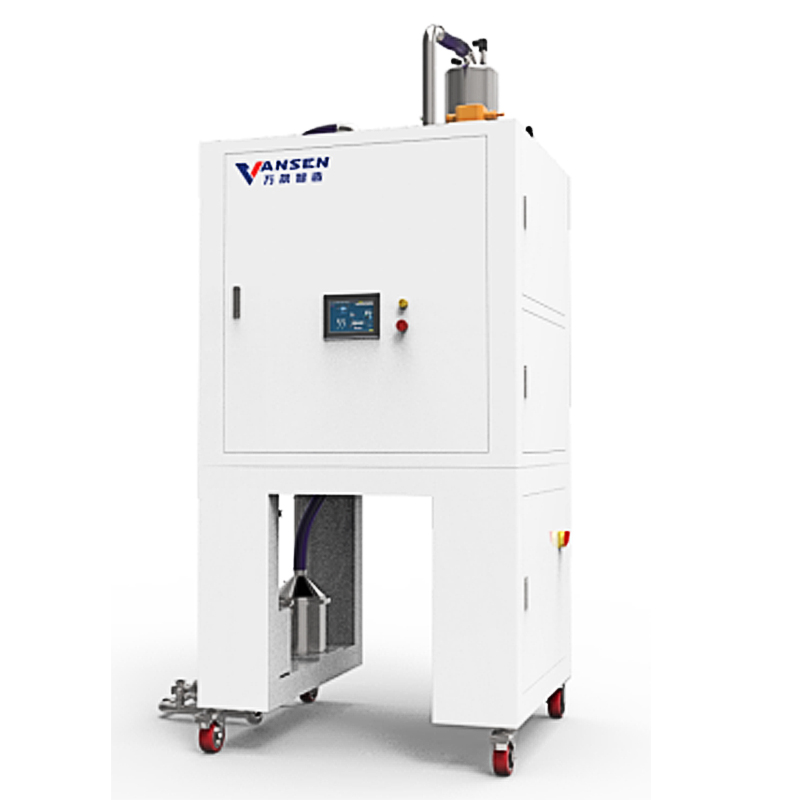
The VSS-V series is equipped with a vacuum suction system and a powder screening system, which combines the suction and screening functions into one, and is an explosion-proof suction and screening machine that performs both functions simultaneously. Not only is the entire conveying and screening process sealed, with no dust leakage, ensuring efficient and safe handling of powders, it also saves space and improves the convenience of operation.
4. Powder feeding machine
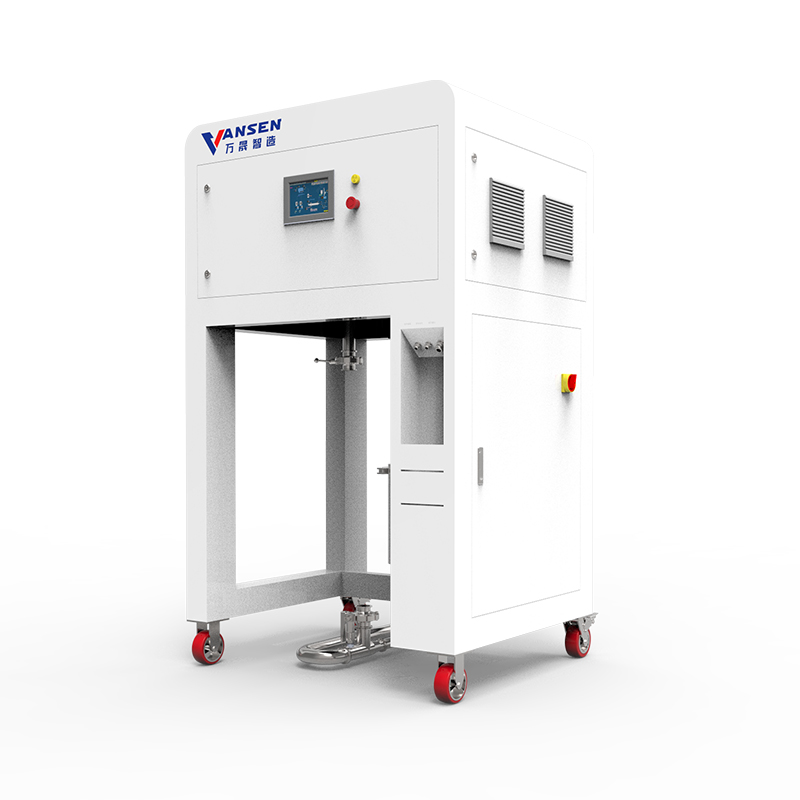
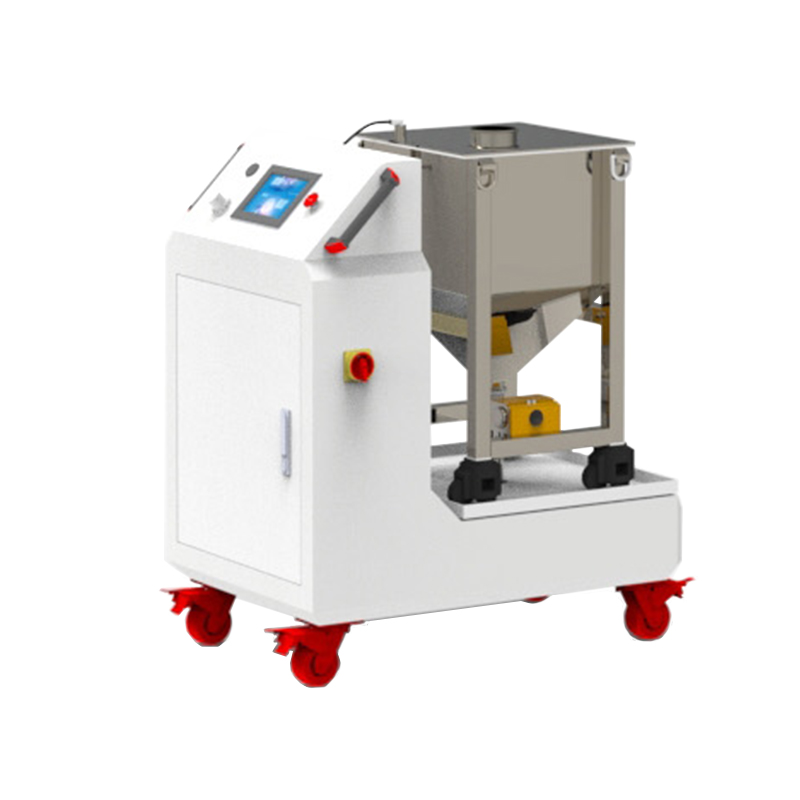
The powder feeder can ensure that the powder is supplied to the print chamber at a stable and uniform flow rate, which is critical to maintaining the consistency and repeatability of the printing process. Wansheng has developed the following two types of powder delivery equipment according to different usage environments:
The negative pressure closed loop, inert gas protection VPS-V series has explosion-proof certification and a wide range of applications, suitable for high-temperature alloys such as stainless steel and mold steel, as well as low-temperature alloys such as aluminum alloy and titanium alloy.
Positive pressure open loop, pneumatic open loop powder feeder, quantitative powder delivery, high efficiency and energy saving, introduces inert gas as power, suitable for high temperature alloys such as stainless steel and mold steel.
5. Feeder
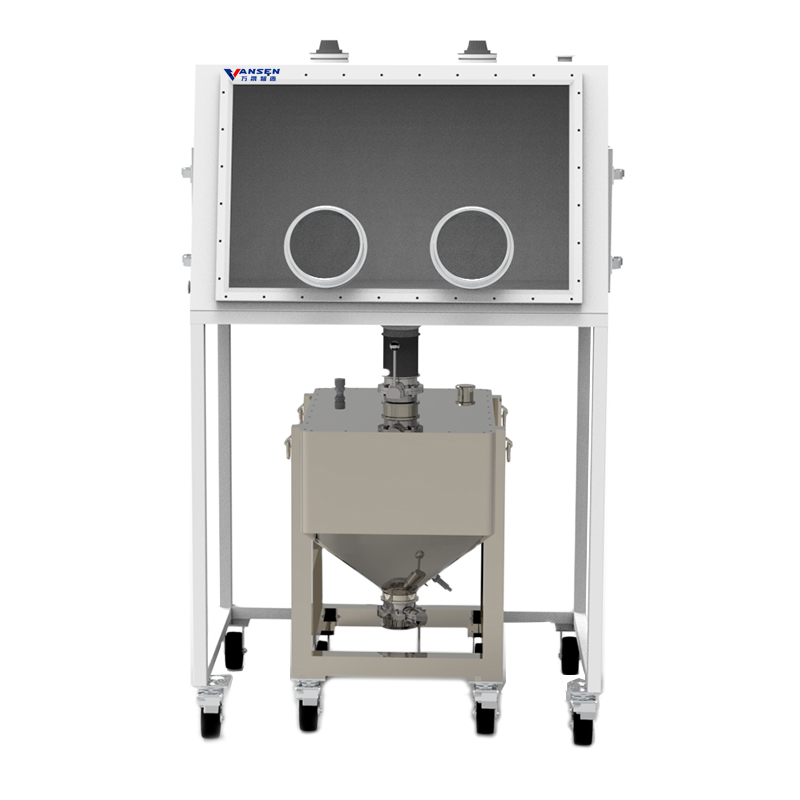
Developed for the disassembly and transportation of small bags of metal 3D printing powder, the sealed box effectively isolates the powder and can effectively avoid dust and spillage during the disassembly and installation of new powder. This design aims to simplify the operation process, reduce manual intervention, save operation and maintenance costs, and improve overall production efficiency.
6. Dryer
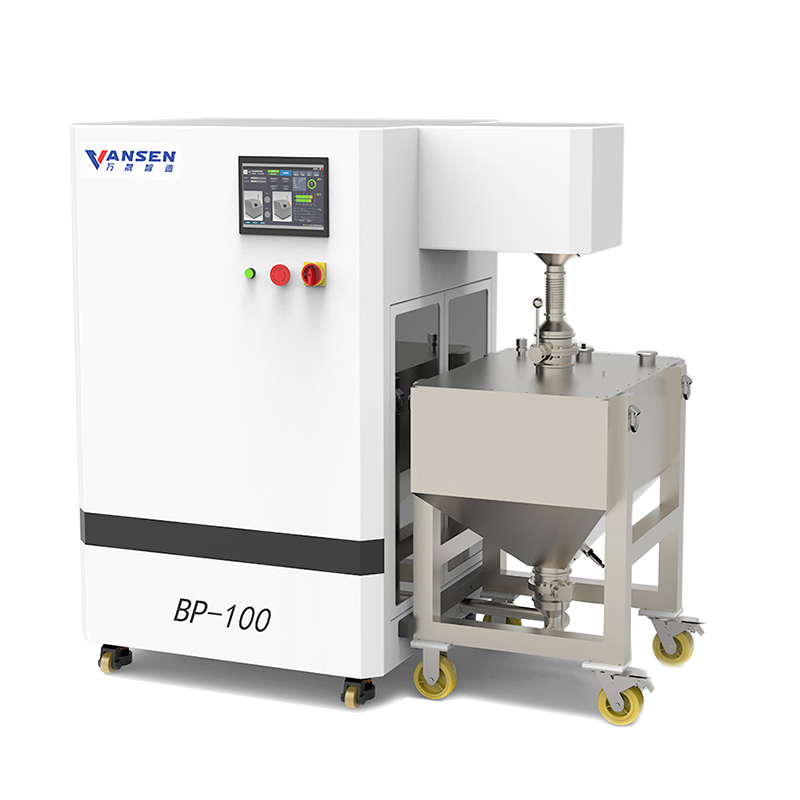
Wansheng has developed a metal powder drying equipment with explosion-proof, automatic drying and customized solutions. The vacuum pump is used to deliver the metal powder to the drying tank. Customized drying solutions are used according to different powders to efficiently remove moisture from the powder by heating and evaporation to prevent quality defects of the printed product caused by moisture, such as bubbles and cracks.
The powder circulation management solution composed of these devices forms a closed-loop powder management system. From powder recovery, screening, drying to reuse, each step has been carefully designed to ensure the best performance of the powder and the highest quality of the printed parts. This not only improves production efficiency and reduces operating costs, but also achieves environmentally friendly production by reducing material waste.
Wansheng Intelligent Manufacturing has many years of experience in non-standard customized professional equipment and is committed to providing customers with the highest quality products and services. This solution has production advantages such as improving printing quality, reducing costs, improving efficiency, shortening production cycles, etc., truly solving customer needs in one stop.